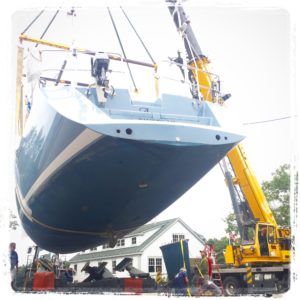
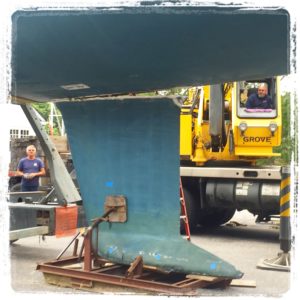
Even familiar waters can catch a good sailor off guard. This certainly proved true for the skipper of a Westerly 57, when he accidentally “found bottom” in Penobscot Bay last August. Needing to evaluate the extent of the damage caused by the grounding, and wanting to tackle the necessary work promptly, the skipper’s first move was to get the boat to Great Island Boat Yard, his preferred storage and service port. On arrival, the boat was hauled and carefully surveyed.
The initial findings made it clear, this had been a hard hit and the boat would need extensive repairs. The project would require clear communication and careful documentation. With both the boat owner and insurance company on board, GIBY was granted the repair job and a formal plan was put in motion. The goal? Make the boat structurally sound again, and get her back in the water by spring. With these things in mind, the GIBY crew got to work.
First, thermal imaging and hull sounding methods were used to identify the fractured areas. Combining these two methods allowed the team to identify areas of specific damage. Accurate damage evaluation was critical to the success of the project, as it allowed the team to minimize how much cabinetry they would removed from the interior. By removing only what was necessary, the team would save a significant amount of time and labor on the job.
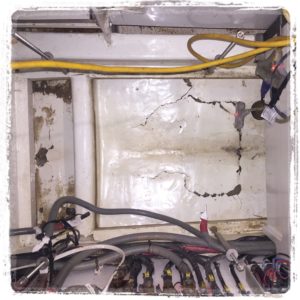
To get the project rolling, the keel was prepped, pulled, and shipped to Rhode Island for straightening and keel bolt replacement. Next, the boat was rolled into the GIBY Refit Bay, a space that could be fully dedicated to the project.
Once settled in for her long winter’s nap, a careful gutting of the boat’s interior commenced. Gaining access to the damaged areas, deep in the belly of the boat, proved labor intensive. Carpenters removed identified cabinetry, bulkheads, and sections of the cabin sole. Tanks, systems, batteries, wires, and hoses were also removed, or relocated, in the effort to expose every micro fracture and every broken stringer.
It was discovered that the impact to the main bulkhead had fractured the keel grid, including the longitudinal and latitudinal stringers. With broken bonds, these were left loosely clinging to the hull. On either side of the keel, two large areas of the hull had also delaminated from the compression of the keel strike. All of these damaged components needed to be replaced.
Once interior access was gained, the delaminated grid tabbing was cut away and the stringers were futher evaluated. It turns out that the original stringers were filled with a low density foam that relied on the strength of the surrounding glass laminate for their structure.
“We replaced the stringers with a high-density, polyurethane foam-reinforced board and then wrapped the grid in fiberglass,” explains Trevor, GIBY’s Operations Manager. “The entire FRP repair was done using epoxy. Epoxy is well known for its strength and secondary bonding characteristics. The two delaminated hull sections were excavated and the damaged coring was replaced with new material laminated securely to the hull.”
Throughout the project, just one half of the boat was worked at a time. This allowed for large pieces (such as fuel tanks too large to be removed from the boat) to be shifted out of the way within the cabin space. The juggle for elbow room complicated the job, but the crew’s careful planning made it all manageable. When complete, the entire bilge area was sanded, faired smooth, and coated with a high-gloss white finish. Today, the bilge looks brand new; and, going forward, it will also be easier for the boat owner to visually monitor while underway.
Now, as the various tanks, systems, batteries, wires, and hoses are put back in place, the many pictures and notes taken during disassembly will serve as critical references. Soon the carpentry team will reinstall the built-ins and the cabin sole, and the boat will be returned to the owner, as good as new, ready for her next sailing adventure!
Leave a Reply