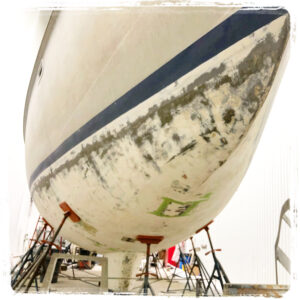
Careful preparation is key to successful yacht finish work, but never is this more true than in the case of preparing aluminum surfaces. This winter, painting the decks and bottom of an aluminum Kanter 54 has provided our crew with some interesting challenges. To execute, the preparation efforts started long before the boat entered the GIBY Paint Bay.
“There were three unique elements to this job,” says Trevor Davis, GIBY’s Operations Manager. “The first was that the corrosion needed to be 100% removed prior to coating, to ensure total adhesion between the aluminum deck, fairing materials, and paint. The second was that the bare aluminum needed to be managed after the media blasting, to keep it from oxidizing. And the third was to control the blast media, to keep it from entering and contaminating the boat’s finished interior spaces.”
To manage and move beyond each of these obstacles, a significant team effort was made to prepare the boat for GIBY’s painters.
“We opted to extensively media blast and acid-wash the corroded areas,” says Trevor. “Media blasting the decks exposed deep crevasse corrosion that would not have been accessible with grinding or sanding tools alone. To address the short oxidation period after blasting, we coated the bare aluminum areas with acid to quickly remove any oxidized surfaces. The phosphoric acid cleaner ensures a clean, oxidation-free surface suitable for painting.”
Controlling the blast media was an equally tricky and important part of the job.
“Because all the deck hardware, hatches, and windows were removed to access the corrosion below them, we had to utilize a large array of rubber plugs, interior mounted plywood window and hatch covers, and set screws to close up even the smallest of holes,” says Trevor.
With the team’s commitment to proper preparation and attention to detail, the boat is now being primed, prepared with high-build, dye-coated, faired, primed again, and finished with Awlgrip. The next challenge will be to reassemble the boat, isolating every piece of stainless-steel hardware, in a manner that keeps dissimilar metals apart and prevents future risk of corrosion.
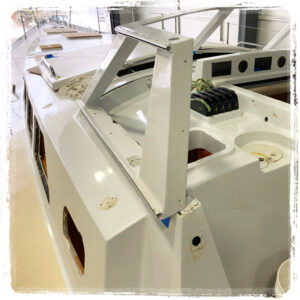
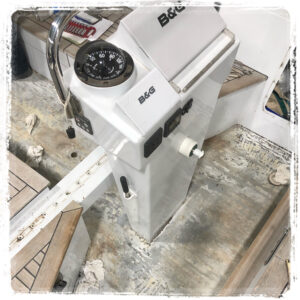

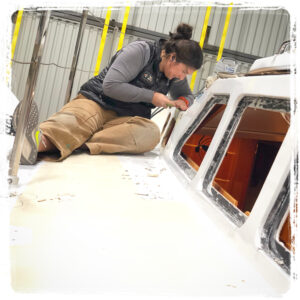
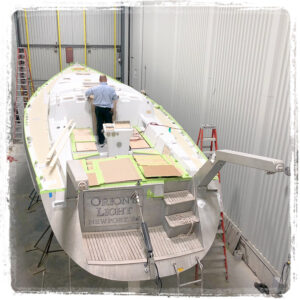
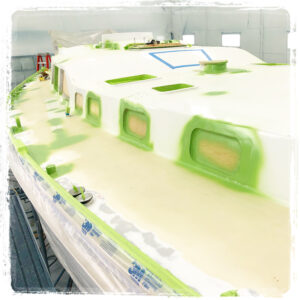
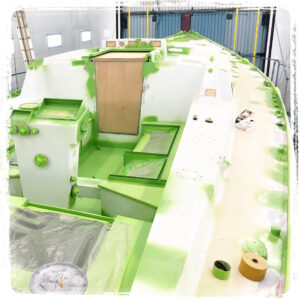
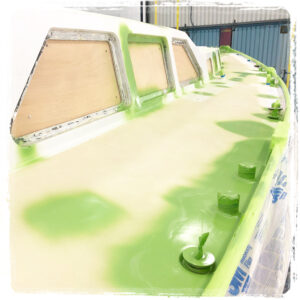
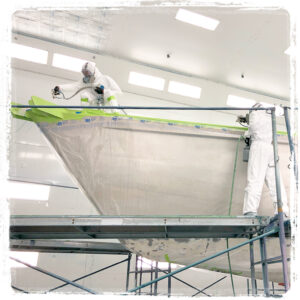
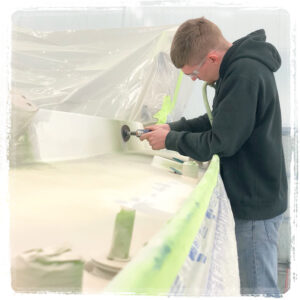
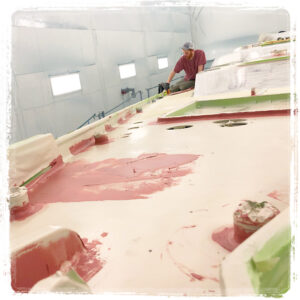
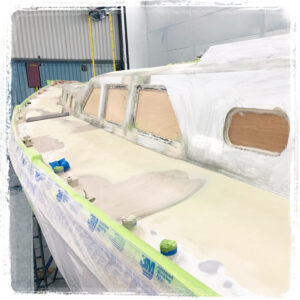
Leave a Reply